TPM UTRZYMANIE RUCHU – METODA, Z KTÓRĄ POWINNA ZAPOZNAĆ SIĘ KAŻDA FIRMA PRODUKCYJNA
CZYM JEST TPM?
Chcąc dosłownie przetłumaczyć z języka angielskiego skrót TPM (Total Productive Maintenance), otrzyma się „Totalne Utrzymanie Ruchu”. Nie do końca brzmi to dobrze, dlatego w Polsce ten skrót tłumaczy się jako: „Kompleksowe (efektywne) utrzymanie ruchu”. Jaka jest zatem definicja tpm?
Jak podaje najpopularniejsza encyklopedia internetowa, TPM to jedna z metod stosowanych w odchudzonym zarządzaniu, czyli Lean management. Metoda tpm ma na celu zapewnienie jak największej efektywności maszyn i urządzeń. Pod hasłem ”efektywność”, kryje się maksymalne wykorzystanie czasu pracy maszyn, w celu wykonania planu produkcyjnego.
System kompleksowego utrzymania ruchu wywodzi się oczywiście z Japonii, gdzie powstał cały Lean management (pionierem wśród firm, gdzie utrzymanie ruchu zadziałało, jest Toyota). TPM tak naprawdę polega na odpowiedniej obsłudze maszyn i urządzeń – ich konserwacji i zorganizowanej, określonej pracy, i diagnozie różnych zdarzeń mających miejsce podczas pracy maszyny. Całe przedsięwzięcie realizowane jest wewnątrz przedsiębiorstwa a dokonują go operatorzy tych maszyn (jest tak zwane autonomiczne utrzymanie ruchu) oraz personel odpowiedzialny za utrzymanie ruchu (nazywane jest tp planową konserwacją). Dzięki zorganizowaniu i doskonałej współpracy pomiędzy produkcją a działem utrzymania ruchu, możliwa jest poprawa efektywności nawet najbardziej wyeksploatowanego parku maszynowego. TPM pozwala również zmniejszyć awaryjność czy niepotrzebne mikroprzestoje pracy maszyn.
Kiedy firma zaczyna swoją działalność, zwykle należy do małych przedsiębiorstw. Zatrudnia maksymalnie kilka osób i pomału stawia swoje kroki na rynku. Z czasem, zyski firmy rosną a ona rozwija swoje skrzydła. W pewnym momencie dochodzi do momentu, kiedy już nie jest ani małym, ani średnim przedsiębiorstwem – staje się potężną firmą. Firmą, w której zwykle zaczynają powstawać problemy z dostępnością parku maszynowego. I tutaj z pomocą przychodzi właśnie TPM . Czym ten program jest? ? O tym w dalszej części tekstu.
Cele TPM
Utrzymanie ruchu z definicji pozwala na:
- wydłużenie czasu eksploatacji urządzeń i maszyn,
- mierzenie efektywności całego parku maszynowego,
- zapewnienie płynności pracy maszyn, urządzeń i całej linii produkcyjnej,
- redukcję awarii maszyn i urządzeń,
- zwiększenie prędkości pracy maszyn i urządzeń,
- eliminowanie niepotrzebnych mikroprzestojów,
- polepszenie wyników finansowych przedsiębiorstwa, dzięki odpowiedniemu zarządzaniu.
Powyżej wymienione podpunkty, składają się na cele utrzymania ruchu. Dlaczego? Dlatego, że głównym powodem wprowadzenia metody TPM jest maksymalne zwiększenie stabilności procesów występujących podczas każdorazowej produkcji. Celem jest również wydłużenie żywotności maszyn czy obniżenie kosztów związanych z utrzymaniem tych maszyn i urządzeń (konserwacje, przeglądy, serwisy – wszystko to sprawia, że koszt amortyzacji jest naprawdę wysoki). Podsumowując – metoda TPM dąży do tego, by firma osiągnęła poziom trzech zer: zero braków, zero awarii, zero wypadków przy pracy.
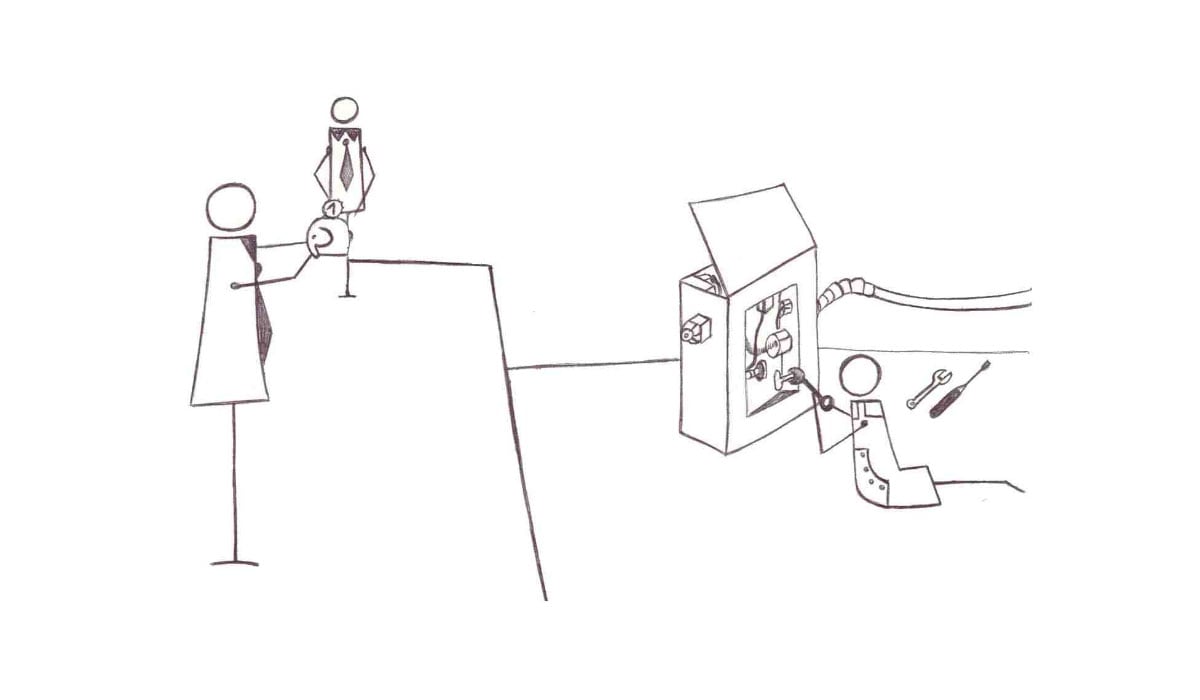
Zaletą takiego rozwiązania jest to, że do “starych” maszyn i urządzeń pracownicy są przyzwyczajeni. Znają ich obsługę, wiedzą co mają robić i jak postępować. Poprawa efektywności może więc być natychmiastowa, jeśli odpowiednio wdroży się TPM do przedsiębiorstwa. Inaczej jest w przypadku nowych maszyn. Dlaczego? Dlatego, że wówczas pracownicy nie mają wiedzy, kompetencji i doświadczenia w pracy na nowych urządzeniach. To z kolei wiąże się ze zdobywaniem doświadczenia – a więc czasem..
Drugą płaszczyzną jest człowiek – przecież to on odpowiada za całą produkcję. Wprowadzenie TPM , pozwoli na efektywniejszą pracę pracowników. Jak to możliwe? Otóż organizacja działu utrzymania ruchu w głównej mierze oparta jest na odpowiednim szkoleniu. Na takim kursie, pracownicy poszerzają swoją wiedzę z zakresu planowania produkcji i działania maszyn. Stają się bardziej odpowiedzialni i mocniej się angażują w swoją pracę i rozwiązywanie problemów . Szkolenie uczy ich, jak postępować w momencie nietypowej sytuacji, kiedy konieczne jest podjęcie szybkiej i pewnej decyzji.
Niestety, jeśli nie będzie odpowiedniej komunikacji i współpracy między utrzymaniem ruchu a produkcją, na nic się zdadzą wszelkie szkolenia. Aby wdrożenie TPM miało sens, trzeba działać wspólnie. Trzeba przekazywać informacje o stanie parku maszynowego, o problemach, o usterkach. Należy regularnie kontrolować i konserwować maszyny i urządzenia, by nie dopuścić do ich zepsucia. Takie działanie powoduje, że służby utrzymania ruchu płynnie przechodzą z obsługi reakcyjnej (opartej na reakcjach, przeczuciach, nawykach) na obsługę prewencyjną (polegającą na zaznajomieniu się z maszyną, poznaniu jej dokładnego działania i przede wszystkim na “wyprzedzaniu” powstawania ewentualnych postojów).
Takie działanie pozwala zmniejszyć koszty, zwiększyć zyski i osiągnąć zamierzone cele. Pozwala również uniknąć szesnastu typowym strat w procesie produkcji, którymi są:
Straty dostępności:
- awarie,
- wyłączenia,
- regulacje, ustawienia,
- braki, poprawki,
- przezbrojenia,
- straty szybkości,
- drobne przestoje,
- uruchomienia.
Straty skuteczności:
- zarządzania,
- ruchu,
- organizacji linii,
- logistyki,
- pomiarów i regulacji.
Straty produkcji:
- energii,
- oprzyrządowania,
- wydajności.
Dzięki wprowadzeniu kompleksowego utrzymania ruchu, pracownicy stale polepszają obszary swojej działalności. Produktywność przedsiębiorstwa wyraźnie się poprawia.
Filary TPM
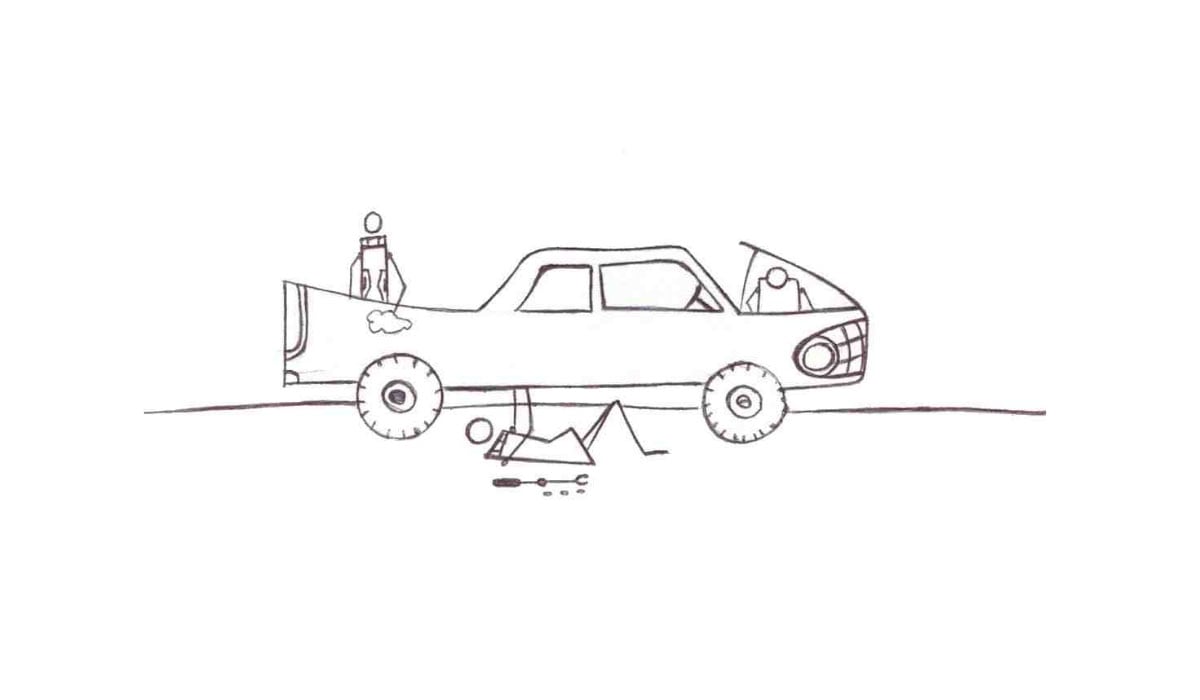
Cała koncepcja japońskiej metody utrzymania ruchu na zasadach TPM, opiera się na ośmiu filarach. Są one swego rodzaju podporą dla całego systemu. Co zatem składa się na każdy z nich?
-
- Filar pierwszy – Autonomiczne Utrzymanie Produkcji / z angielskiego: l Autonomous Maintenance /
Filar ten jest oparty na wiedzy operatorów odnośnie maszyn, które obsługują. Ze względu na to, że pracownik na co dzień współpracuje z daną maszyną, poznaje ją od środka a dzięki temu na wczesnym etapie jest w stanie wykryć różne nieprawidłowości. Pracownik bardzo szybko rozpozna niepokojące stukanie, hałas, skrzypienie, tarcie – czyli wszystko to, co może wskazywać, że maszyna za chwilę może ulec awarii. Jest to pewnego rodzaju odniesienie do bycia kierowcą i codzienniej eksploatacji samochodu.
Na pierwszy filar składa się siedem, kolejnych etapów:
-
-
- początkowe czyszczenie, które jest połączone ze rozpoznaniem anomalii działania maszyny, (ma to bardzo duży związek z drugim programu 5S)
- eliminacja błędów i przyczyn ich powstawania,
- czyszczenie i smarowanie – standardowe, rutynowe działania, które wykonują zarówno specjaliści, jak i pracownicy produkcyjni,
- ogólny przegląd – pracownicy produkcyjni muszą zostać przeszkoleni w kierunku standardowych działań przejmowanych od specjalistów,
- samodzielny przegląd – realizacja standardów czyszczenia i przeglądów otrzymanych na szkoleniu w praktyce,
- zarządzanie obszarem – poprawa stanu maszyn i urządzeń,
- samodzielne utrzymanie – standaryzacja działań, drobne naprawy.
-
Autonomiczne utrzymanie ruchu pozwala operatorom na wczesne wykrycie nieprawidłowości. Celem pracowników – w myśl filaru pierwszego – jest jak najwcześniejsze zidentyfikowanie i eliminacja przyczyn zmienności w wydajności maszyn i urządzeń, a także nieustanne dążenie do poprawy wydajności. Do tych celów można zaliczyć także zwiększenie udziału pracowników w utrzymaniu ruchu tam, gdzie wykonują swoją pracę czy zwiększenie odpowiedzialności wśród operatorów za stan techniczny ich urządzeń i maszyn, z którymi na co dzień współpracują. Dzięki autonomicznemu utrzymaniu ruchu pracownik jest bardziej związany z maszyną przez co poprawia się jakość stanowiska pracy a same umiejętności operatorów stają się coraz lepsze. Wszystkie te działania prowadzą do tego, by zintegrować ze sobą dział produkcji z działem utrzymani ruchu.
-
- Filar drugi – Doskonalenie Kaizen / z angielskiego: Focus Improvement /
Filar ten opiera się na metodzie Kaizen, czyli na założeniu, że efektywność firmy wzrośnie pomimo że udoskonalenie procesu będzie niskonakładowe. Co to oznacza? Mianowicie chodzi o to, by stale doskonalić procesy i organizację miejsca pracy. Jest to możliwe tylko wówczas, gdy pracownicy angażują się w obowiązki i wspólnie pracują na to, by zdobywać coraz wyższe standardy ich pracy.
Punktem wyjściowym tego filaru jest dokładne rozpoznanie potrzeb i problemów, które wynikają z wykonywanej pracy. Jeżeli pracownicy nie wiedzą nic o zaistniałych problemach, nie będzie możliwe wprowadzenie działań, których celem byłoby udoskonalenie procesu. Stąd też metoda Kaizen zawarta jest w tym filarze. Dzięki niej, przedsiębiorstwo stawia nacisk na poszukiwanie źródeł wszystkich problemów, a do ich znalezienia wykorzystuje narzędzia TPM, czyli na przykład: diagram Ishikawy, diagram Pareto-Lorenza czy 5W.
-
- Filar trzeci – Planowane Utrzymanie Ruchu / z angielskiego: Planned Maintenance /
Ten filar opiera się na zadaniach, wynikających z planowanych działań utrzymania ruchu. Zadania te mają wyeliminować awarie i mikroprzestoje maszyn. Zakres działań obejmuje przede wszystkim analiza powstałych usterek oraz określenie środków zapobiegawczych. Jednak to nie wszystko. Planowane Utrzymanie Ruchu to również zarządzanie smarowaniem, wymiana zużytych podzespołów i części maszyn. To także zarządzanie kosztami utrzymania, regulacją i skrócenie czasu napraw.
Kiedy pracownicy znają codzienną pracę maszyn, szybko będzie można wykryć wszelkie nieprawidłowości w przyszłości. To z kolei pozwoli na planowaną konserwację, naprawę. Dodatkowo, Dział Utrzymania Ruchu, posiadając jasno określone terminy, będzie mógł zaplanować całą współpracę z Działem Produkcji, by wspólnie walczyć o najwyższe wskaźniki utrzymania ruchu: OEE (Całkowita Efektywność Wyposażenia / z angielskiego: Overall Equipment Effectiveness) oraz OPE (Całkowita Efektywność Zakładu / z angielskiego: Overall Plant Effectiveness).
-
- Filar czwarty – Utrzymanie Dla Jakości / z angielskiego: Maintenance For Quality /
Filar ten opiera się na identyfikacji warunków produkcji. W głównej mierze w tym kroku należy skupić się na poprawie jakości wyrobów. W jaki sposób? Otóż należy zastosować odpowiednie narzędzia jakości i przeprowadzić analizę wykonywanej na maszynach pracy. W ten sposób będzie można na bieżąco odczytywać powstające błędy, które mogłyby mieć wpływ na produkt finalny.
-
- Filar piąty – Utrzymanie Ruchu w Biurze / z angielskiego: TMP In Office /
Filar ten opiera się na działaniach, które mają prowadzić do doskonalenia procesów zachodzących w pracy biurowej. Przede wszystkim chodzi o przepływ informacji. Bez poprawnej komunikacji w firmie panowałby chaos. Dlatego też powinno się rozmawiać o awaryjności maszyn i urządzeń, skuteczności przeglądów czy o ich faktycznym czasie pracy. W taki sposób, park maszynowy będzie działać bez zarzutu – zero przestojów, zero marnotrawstwa.
-
- Filar szósty – Bezpieczeństwo, Środowisko, Zdrowie / z angielskiego: Safety and Environment /
Filar ten opiera się na wyeliminowaniu zagrożeń dla pracowników oraz środowiska naturalnego. Generalnie w tym kroku należy ograniczyć zużycie materiałów oraz energii. By wdrożyć ten filar, firma musi opracować strategię utrzymania ruchu, czyli odpowiednio zorganizować poszczególne zadania. Przykładowo pracownik Działu Utrzymania Ruchu w swoim zakresie obowiązków powinien mieć między innymi: bieżącą konserwację urządzeń na linii produkcyjnej, usuwanie awarii, nadzór nad sprawnością techniczną urządzeń. Natomiast już mistrz bądź kierownik Działu Utrzymania Ruchu będzie musiał skupić się na zapewnieniu ciągłości produkcyjnej, koordynować i nadzorować bieżącą pracę, zlecać konserwacje i naprawy.
Jeżeli każdy pracownik będzie znał swoje obowiązki i będzie starał się je wykonywać w stu procentach, firma na pewno będzie działać sprawniej, co przełoży się nie tylko na zyski ale i na lepszą jakość produkowanych wyrobów.
-
- Filar siódmy – Szkolenia / z angielskiego: Training /
Filar ten opiera się na nauce i to ciągłej, cyklicznej. Rozwój jest tutaj naprawdę bardzo istotny – przede wszystkim ze względu na bardzo szybki postęp technologiczny. Poszerzanie umiejętności i zdobywanie wiedzy technicznej, obejmuje zakresem pracę zespołową oraz zarządzanie w sytuacjach problemowych. Takie szkolenia powinni odbywać wszyscy pracownicy – a nie tylko inżynier, specjalista czy technik utrzymania ruchu.
-
- Filar ósmy – Metoda 5S /
Filar ten stanowi fundament pozostałych siedmiu. Jest to narzędzie, które służy ciągłemu doskonaleniu, w celu zorganizowania miejsca pracy. Jeżeli przestrzeń robocza jest niezorganizowana , trudno dostrzega się awarie i błędy maszyn. Dodatkowo, w takim bałaganie, często dochodzi do marnotrawstwa materiału oraz czasu pracy, na przykład podczas szukania narzędzia, które nie zostało odłożone na swoje miejsce. Bez wdrożenia metody 5S i bez organizacji Działu Utrzymania Ruchu, przedsiębiorstwo nie osiągnie założonych celów.
Proces wdrożenia TPM
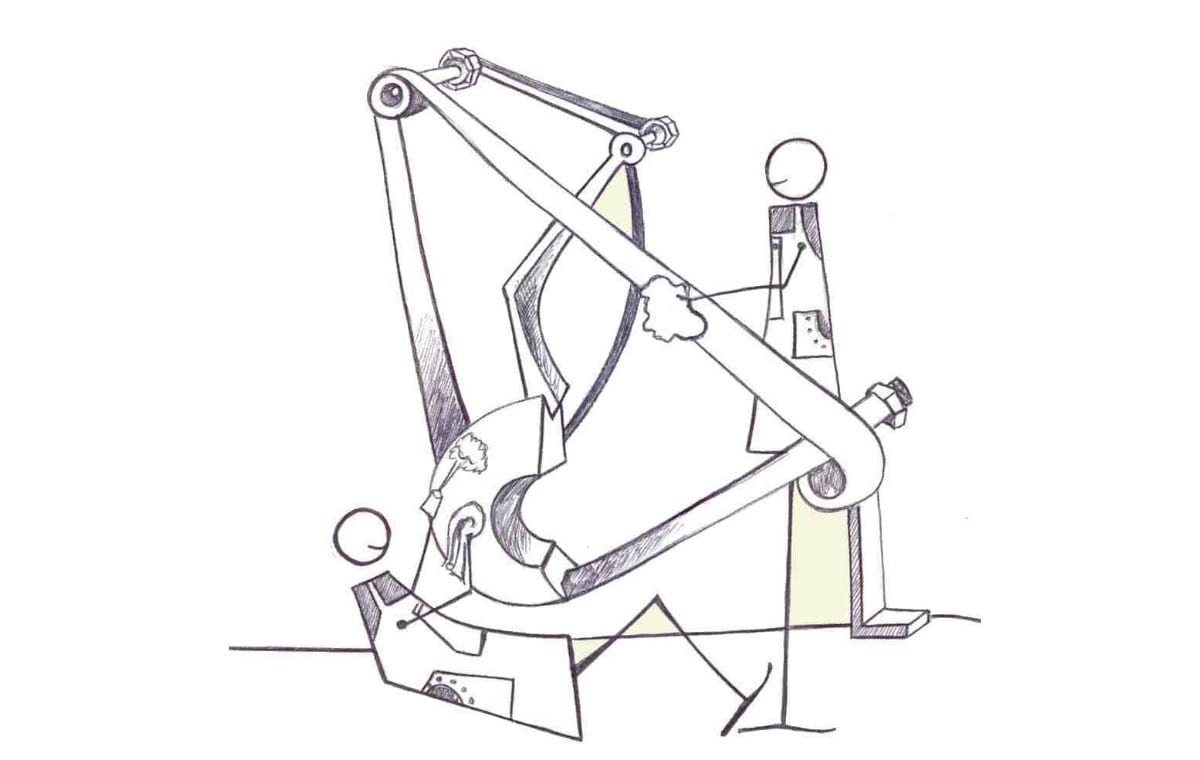
Wdrożenie TPM dzieli się na trzy główne fazy. Pierwsza – narzuca zmianę sposobu myślenia wśród pracowników i dotyczy zarówno kadry zarządzającej , jak i operatorów maszyn, na przykład technika czy automatyka utrzymania ruchu.
Druga faza prowadzi do stworzenia systemu utrzymania ruchu, który opierać się będzie na pracy zespołowej. W tej fazie należy również podjąć działania na rzecz wprowadzenia metody 5S. W tej fazie firmy często korzystają z usług – outsourcingu utrzymania ruchu. Zamówiony serwis utrzymania ruchu szybko usunie niepotrzebne elementy, uporządkuje miejsce pracy. Sprawi, że przestrzeń robocza będzie czysta, schludna i intuicyjna. Dzięki takiemu rozwiązaniu, zarządzanie utrzymaniem ruchu będzie łatwiejsze.
Faza trzecia, to przede wszystkim praca nad wdrożeniem i utrzymaniem metody 5S. Tutaj również odbywają się szkolenia pracowników. Usuwa się awarie, rozwiązuje bieżące problemy. Efektem wdrożenia fazy trzeciej jest między innymi: lepsza wydajność pracy, eliminacja awarii, mniejsza liczba wypadków, mniejszy stopień odpadów a także wzrost zaangażowania się pracowników w powierzone obowiązki.