Lean Games – Revolutionizing Corporate Training with Interactive Simulations
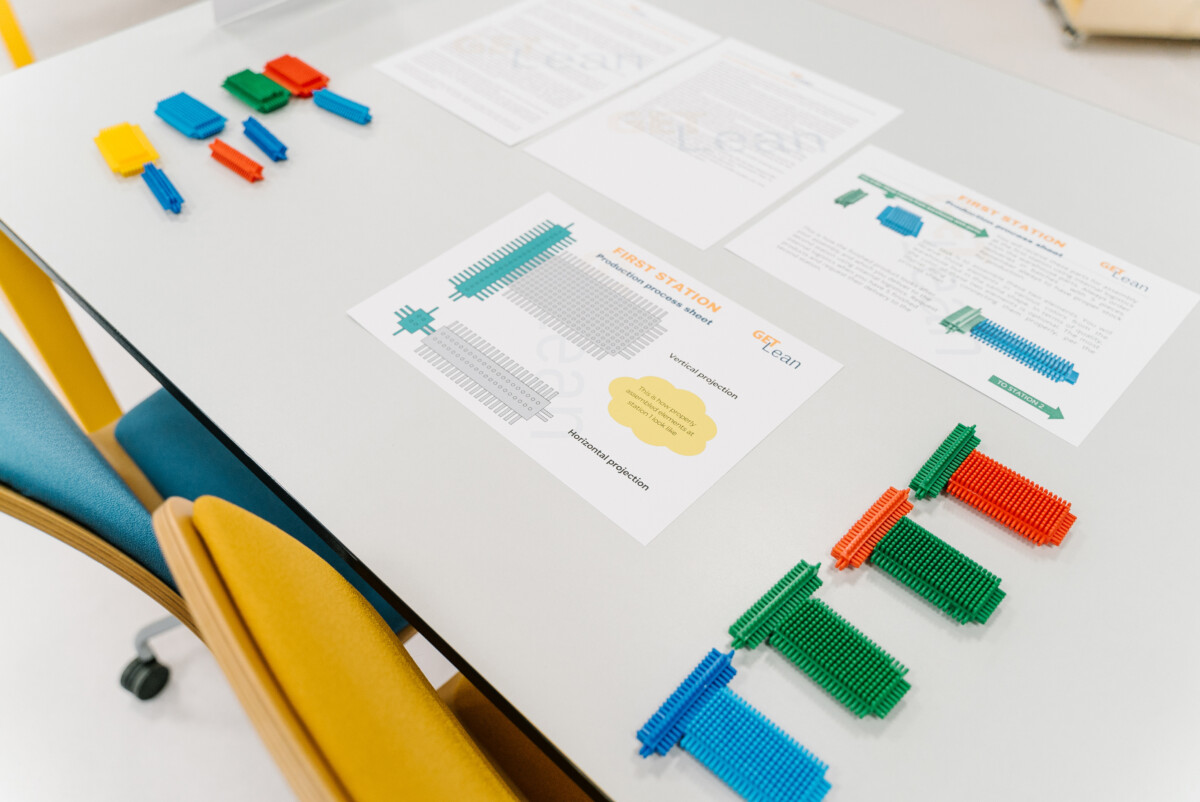
Hands-on learning in action — participants use GET LEAN simulation game tools to visualize production processes and improve team collaboration, which is the best way to learn Lean principles.
1. Introduction to Lean Games
In today’s fast-paced and competitive business environment, organizations are under continuous pressure to optimize processes, reduce waste, and foster a culture of ongoing improvement. Traditional training methods, relying on lectures and slide presentations, often fail to engage employees or deliver practical, impactful lessons. This is where lean games—interactive, simulation-based training tools—step in. They provide an engaging way for employees to learn by doing, bridging the gap between theory and real-world application.
Lean games immerse participants in realistic scenarios, enabling them to experiment in a risk-free environment. This experiential learning method accelerates the understanding of concepts, improves knowledge retention, and fosters a proactive, continuous improvement mindset that is vital for complete operational excellence.
2. The Concept and Benefits of Lean Games
2.1. What Are Lean Games?
Lean games are interactive simulations designed to replicate the challenges faced in actual operational environments from the very beginning. They enable employees to apply Lean principles, such as waste elimination, process optimization, and continuous improvement, in a hands-on setting. In these simulations, participants are tasked with making quick, strategic decisions, which provide immediate feedback through performance dashboards and key metrics.
Key features include:
- Realistic Scenarios: Simulations mirror everyday production or service challenges, emphasizing the practical application of Lean principles.
- Interactive Decision-Making: Employees actively participate in problem solving, which improves engagement and learning retention.
- Collaborative Learning: Many lean games require team-based problem solving that enhances cross-functional communication and collaboration.
- Safe Experimentation: The controlled, virtual environment allows employees to test new ideas without the risk of real-world consequences.
2.2. The Benefits of Lean Games
Lean games offer several advantages over traditional training methods:
- Enhanced Engagement and Retention: Active participation makes lean games highly engaging, improving retention of Lean concepts and principles.
- Accelerated Decision-Making: Time-bound scenarios help participants develop quick, informed decision-making skills essential in fast-paced operational environments.
- Safe Space for Experimentation: The risk-free nature of lean games encourages innovative problem solving and a growth mindset by allowing employees to learn from their mistakes without real-world repercussions.
- Improved Teamwork and Collaboration: By fostering teamwork, lean games help break down silos and promote a unified effort towards achieving continuous improvement.
- Operational Efficiency and Waste Reduction: Through simulation, employees learn to identify and eliminate inefficiencies, which directly translates into cost savings and improved productivity as waste is eliminated.
For a deeper perspective on how simulation-based learning can drive effective training, explore simulation-based learning and discover how gamification boosts workplace performance.
3. Types and Structure of Lean Games
3.1. Types of Games
Lean games come in various forms, each designed to teach specific Lean principles through engaging, hands-on activities. One popular type is the Lean Lego game, which uses Lego bricks to demonstrate concepts like waste reduction, one-piece flow, and standard work. Participants build and modify Lego structures, learning to identify inefficiencies and optimize processes in a fun, interactive way.
In the realm of software development, Lean games often focus on Agile and Scrum methodologies. These games simulate project management scenarios, helping teams understand the importance of iterative development, continuous improvement, and effective communication.
Other types of Lean games include production line simulations and supply chain management games. These simulations replicate real-world operational challenges, allowing participants to experiment with Lean techniques like pull systems and kanban. By engaging in these diverse exercises, team members gain a comprehensive understanding of Lean principles and how to apply them in various contexts.
3.2. Game Structure
The structure of a Lean game is crucial for its effectiveness in teaching Lean principles. Typically, a Lean game begins with an introduction that sets the stage and explains the objectives. Participants are then given a set of instructions to guide them through the game.
A common format is to divide the game into rounds, such as the four rounds in a typical Lean Lego game. Each round builds on the previous one, gradually introducing more complex concepts and challenges. For example, the first round might focus on identifying waste, while subsequent rounds demonstrate techniques like one-piece flow and pull systems.
Participants often assume various roles within the game, such as team leaders, suppliers, and customers. This role-playing aspect helps simulate real-world scenarios and encourages cross-functional collaboration. By following a structured approach, Lean games effectively demonstrate the benefits of Lean manufacturing and promote continuous improvement.
3. Best Practices for Implementing Lean Games
3.1. Start with a Needs Assessment
A successful lean game program begins with a thorough understanding of your organization’s challenges, making sure all stakeholders are aware of potential issues:
- Identify Process Gaps: Analyze your operations to pinpoint inefficiencies, bottlenecks, or quality issues.
- Set Clear Objectives: Define measurable goals, such as reducing cycle times or lowering defect rates.
- Engage Stakeholders: Involve both leadership and frontline employees to ensure the training addresses real, impactful challenges.
3.2. Customize the Simulation
Lean games should be developed and tailored to your organization’s specific context:
- Adapt Scenarios: Modify the simulation to mirror your operational realities and industry-specific challenges.
- Align Metrics: Adjust performance indicators within the simulation to reflect your company’s key performance goals.
- Integrate Company Data: Where possible, use your own process data to enhance the simulation’s realism and relevance.
3.3. Launch a Pilot Program
Before full-scale implementation, it must be decided to conduct a pilot:
- Select a Representative Team: Choose participants from various departments to gather diverse insights.
- Run Multiple Cycles: Allow enough iterations to thoroughly test and refine the simulation.
- Debrief and Refine: Hold structured debrief sessions to collect feedback, analyze outcomes, and plan improvements.
3.4. Scale and Standardize
Once your pilot program is successful:
- Gradually Expand: Roll out the simulation across suitable departments or locations.
- Integrate with Existing Training: Combine lean games with traditional training methods for a blended learning approach.
- Monitor and Adjust: Continuously track performance metrics and adjust the simulation to maintain alignment with organizational objectives.
5. Overcoming Challenges in Lean Game Implementation
Implementing Lean games can present several challenges, especially for organizations new to Lean manufacturing. One common hurdle is getting team members to buy into the game and take it seriously. To address this, it’s important to emphasize the game’s role in improving customer satisfaction and reducing waste. Highlighting real-world success stories and potential benefits can help motivate participants.
Another challenge is ensuring the game is relevant and applicable to the organization’s specific needs. Customization is key here. By tailoring the game to reflect your unique processes and goals, you can make the learning experience more meaningful. Involving team members in the design and development process also fosters a sense of ownership and engagement.
Providing a fun and interactive learning environment is crucial. Lean games should be enjoyable, encouraging participants to experiment and learn from their mistakes. By overcoming these challenges, organizations can successfully implement Lean games and achieve significant improvements in efficiency and productivity.
4. Get Lean – Our Proven Lean Game Solution
4.1. The Genesis of Get Lean
Our journey to develop Get Lean spanned several years of hands-on Lean Manufacturing and Lean Six Sigma projects, recognizing the differences between traditional training methods and practical application. We recognized that traditional training methods could not fully bridge the gap between theory and practice. Through extensive real-world experience, we designed Get Lean to effectively integrate Lean, Six Sigma, and 5S principles into one comprehensive simulation.
4.2. How Get Lean Works
Get Lean is built to provide an immersive, interactive experience that empowers employees to tackle real operational challenges head-on:
- Realistic Production Environments: Players are immersed in simulated production scenarios that mimic the complexities of actual operations.
- Time-Pressured Decision-Making: The game consists of multiple rounds where rapid, strategic decisions are critical to improving performance metrics, including analyzing actions like crossing the table to identify inefficiencies.
- Real-Time Feedback: Integrated dashboards provide immediate visual feedback on key performance indicators, such as cycle times, defect rates, and throughput.
- Collaborative Role-Based Gameplay: Participants assume specific roles, ensuring cross-functional collaboration and the development of practical problem-solving skills.
- Integrated Lean, Six Sigma, and 5S Methodologies: The simulation uniquely blends various continuous improvement tools, challenging players to optimize workflows, reduce variation, and maintain organized workspaces.
4.3. Proven Results from Get Lean
Our extensive testing and real-world application have demonstrated significant benefits, including improved sales through better client interactions:
- Waste Reduction: Participants learn to identify inefficiencies and reduce waste, leading to improved resource utilization.
- Productivity Improvement: By streamlining operations and optimizing workflows, teams experience faster cycle times and higher overall productivity.
- Enhanced Team Collaboration: The role-based structure and collaborative challenges foster stronger teamwork and better communication across departments.
- Cultural Transformation: Through iterative learning and structured debriefing, Get Lean instills a lasting commitment to continuous improvement and operational excellence.
To explore tailored solutions that meet your organization’s specific needs, please visit our Advanced Lean Simulation Customization page.
5. Integrating Lean Games into Your Corporate Training
5.1. Conducting a Comprehensive Needs Assessment
Begin by identifying the core operational challenges within your organization and keeping a record of inefficiencies:
- Analyze Inefficiencies: Look for common bottlenecks and areas of waste.
- Set Clear, Measurable Goals: Define what you want to achieve through lean game training.
- Involve Stakeholders: Ensure that both management and frontline employees contribute to the planning process.
5.2. Customizing Your Simulation
Tailor your lean game to reflect your operational context:
- Adapt Scenarios: Modify game content to mirror your specific production processes, using materials like paper to simulate real processes.
- Align Objectives: Set performance metrics that match your strategic goals.
- Integrate Real Data: Enhance realism by incorporating your operational data into the simulation.
5.3. Pilot and Refine
Implement a pilot program to test and optimize the simulation, allowing participants to draw insights from each iteration:
- Select a Cross-Functional Team: Start with a group representing diverse operational areas.
- Run Multiple Iterations: Allow sufficient rounds for feedback and iterative improvement.
- Debrief and Adjust: Hold structured debrief sessions to refine the simulation based on participant feedback.
5.4. Scaling Up
After a successful pilot:
- Roll Out Gradually: Gradually expand the simulation to additional departments or locations, ensuring each exercise is tailored to specific needs.
- Blend with Traditional Training: Incorporate lean games into a broader training ecosystem.
- Monitor KPIs Continuously: Adjust the training program based on real-time performance metrics.
8. Work Cell Design and Lean Principles in Action
A work cell is a designated area where a team of workers performs a specific set of tasks or processes. In a Lean environment, the design of work cells is critical for promoting efficiency, productivity, and continuous improvement. By applying Lean principles like one-piece flow and standard work, organizations can create work cells that minimize waste, reduce variation, and improve quality.
For instance, a work cell in a manufacturing setting might be designed to produce a specific product or component. Each team member is responsible for a particular task, ensuring a smooth and efficient workflow. Visual management tools, such as diagrams and charts, help keep the process organized and transparent.
Implementing pull systems and kanban within work cells ensures that production is driven by actual demand, reducing overproduction and inventory waste. By continuously monitoring and refining these processes, organizations can achieve significant improvements in productivity, quality, and customer satisfaction.
By putting Lean principles into action through effective work cell design, organizations foster a culture of continuous improvement and operational excellence. This approach not only enhances efficiency but also empowers team members to take ownership of their processes and contribute to ongoing improvements.
6. The Future of Lean Games in Corporate Training
As technology evolves, lean games are set to become even more integral to corporate training, making it easier for participants to play and learn:
- Immersive Technology: Future lean games may leverage VR and AR to create ultra-realistic training experiences.
- Global Training Solutions: Cloud-based, multilingual simulations will support standardized training across global operations.
- Data-Driven Enhancements: AI and real-time analytics will provide deeper insights into performance and facilitate continuous improvements.
- Blended Learning Ecosystems: Combining lean games with traditional training and digital learning modules will create robust, scalable corporate training environments.
7. Conclusion
Lean games are transforming corporate training by turning theoretical concepts into practical, immersive experiences. Our innovative solution, Get Lean, is the culmination of years of real-world Lean Manufacturing, Lean Six Sigma, and 5S projects. It empowers employees to tackle operational challenges, reduce waste, and drive continuous improvement through interactive simulations.
By fostering a safe space for experimentation, providing real-time feedback, and encouraging cross-functional collaboration, Get Lean drives measurable improvements in efficiency, quality, and teamwork. This holistic training approach not only enhances productivity but also instills a lasting culture of continuous improvement.
Ready to transform your organization’s approach to Lean training? Purchase Get Lean Simulation Game today and experience the difference. To learn more about our innovative solution and how it can be tailored to your needs, discover more about the game.
Embrace the future of corporate training with lean games and empower your workforce to achieve sustained competitive advantage.