Game Lean – How Get Lean Empowers Lean Manufacturing Transformation
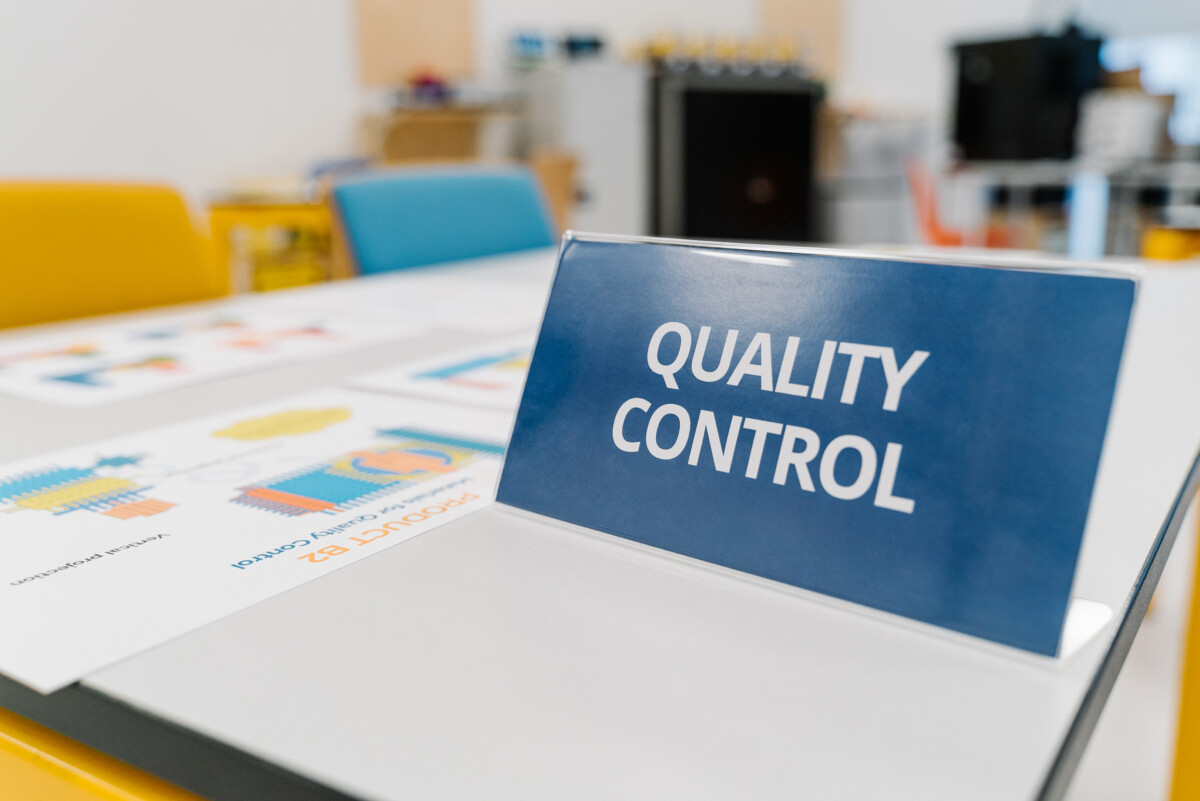
In the game Lean, the aim is to teach principles of lean manufacturing and 5S methodologies by focusing on completing tasks efficiently, understanding the importance of organization, and demonstrating improvements in workplace practices through interactive learning. The Quality Control station teaches how to spot defects and ensure product standards through hands-on simulation.
1. A New Era of Immersive Training
Traditional employee training programs often fail to engage teams or link concepts to real-life applications. Today, organizations are embracing a fresh approach that fuses interactive simulations with proven Lean methodologies. Game lean training is a revolutionary way to immerse employees in a controlled, laboratory-like environment where they can experiment, reflect, and learn to drive continuous improvement in a risk-free setting.
Imagine a training environment where theoretical Lean concepts aren’t just read or heard—they are experienced. In these settings, teams confront realistic process challenges, and every decision prompts visible, immediate outcomes. This method not only boosts engagement but also ensures that the principles of Lean Manufacturing are fully internalized and applied on the job.
Simulation-based training methods offer a dynamic alternative to conventional approaches. They help employees gain practical insights that drive operational excellence, creating a learning environment where continuous improvement is a natural part of everyday work.
2. Understanding Game Lean and Lean Manufacturing Philosophy
2.1. What is Game Lean?
Game lean refers to the application of interactive, simulation-based training, often referred to as a ‘lean game,’ that brings the concepts of Lean Manufacturing into a dynamic, engaging format. Instead of passively receiving information, participants actively engage in decision-making and problem-solving activities that mirror the challenges of their operational environments.
By incorporating real-world simulations, game lean training bridges the gap between theoretical knowledge and practical execution. Employees experience a virtual training scenario where they test ideas, adjust based on immediate feedback, and learn the importance of continuous improvement. This approach transforms abstract Lean concepts into tangible actions that drive measurable results.
2.2. The Philosophy of Lean Manufacturing
Lean Manufacturing is a systematic approach to streamlining operations by eliminating waste, optimizing process flow, and fostering a culture of continuous improvement. Its origins lie in the Toyota Production System, and its core principles include:
- Waste Elimination: Identifying and removing non-value-added activities.
- Flow Optimization: Structuring work processes to ensure smooth, continuous production.
- Pull Systems: Producing goods in response to customer demand, rather than pushing products through the system.
- Continuous Improvement (Kaizen): Encouraging ongoing incremental enhancements across all operational levels.
- Standardization (5S): Creating organized, efficient workspaces through systematic practices.
Lean Manufacturing is not just about reducing costs; it is about creating value for the customer by improving quality, reducing lead times, and enhancing overall efficiency.
Game lean training is designed to deliver these principles in an engaging and efficient way, ensuring that employees understand not only the “how” but also the “why” behind every process improvement.
3. The Role of Simulation in Lean Training
Simulation offers a transformative approach to corporate training. It leverages interactive, hands-on experiences to mirror real-world scenarios. In the context of lean training, simulations create a virtual environment in which employees can safely experiment with process adjustments and immediately see the results of their actions.
3.1. Experiential Learning in a Controlled Environment
The core benefit of simulation-based learning is its emphasis on experiential learning. Employees are not merely passive learners; they actively engage with the content, make decisions, and see the outcomes of their efforts. By playing the simulation, participants gain hands-on experience, enhancing their understanding of Lean principles through interactive and competitive scenarios.
Furthermore, simulation-based learning aligns with modern research on cognitive retention. When learners process information visually, auditorily, and kinesthetically, the comprehension and memory of that information are significantly enhanced. This multisensory engagement accelerates the learning curve far beyond that of traditional methods.
3.2. Immediate Feedback and Iterative Improvement
One of the most powerful features of simulation-based training is the provision of immediate feedback, allowing employees to complete tasks efficiently. In a game lean environment, every decision is closely monitored, and its outcomes are displayed in real-time via performance dashboards. This continuous feedback loop allows employees to quickly adjust their strategies, reinforcing the principles of constant improvement. The iterative nature of simulations means that every round becomes an opportunity to learn, adapt, and refine tactics—a process that embodies the Lean philosophy of Kaizen.
3.3. Psychological Safety for Innovative Experimentation
Fear of failure is a common barrier to the adoption of new processes. Simulation-based training creates a safe space where failure is not punished but viewed as a valuable learning opportunity. This psychological safety encourages employees to take risks, try new approaches, and innovate without fearing real-world consequences. The freedom to experiment is a catalyst for breakthrough ideas and operational improvements.
For more insights into the science behind immersive training, explore simulation-based learning.
4. My 25 Years in Lean Manufacturing: Lessons Learned
Over the past 25 years, I have dedicated my career to implementing Lean Manufacturing principles across a variety of industries. My journey has provided me with a deep understanding of both the potential and the challenges inherent in transforming operational processes.
Throughout my career, I observed that:
- Theoretical Learning Falls Short: Many traditional training programs do not adequately bridge the gap between theory and application.
- Practical Insights are Crucial: Real-world projects demonstrate that the true value of Lean lies in its practical implementation.
- Employee Buy-In is Essential: The more employees understand the tangible benefits of Lean, the more readily they embrace its principles.
These experiences were instrumental in shaping my vision for a more effective training solution—one that would harness the power of simulation to deliver hands-on, practical Lean training that truly makes a difference on the shop floor.
5. The Six-Year Journey to Create Get Lean
Recognizing the limitations of conventional training methods, I committed to developing a simulation game that would effectively transform Lean training. Over nearly six years, I collaborated with industry experts. I leveraged my extensive experience to create Get Lean—a game lean solution designed to simplify the adoption of Lean Manufacturing principles.
5.1. Vision and Objectives
The core vision behind Get Lean was to create an environment where employees could:
- Experience Lean in Action: See how Lean principles, when implemented correctly, lead to significant improvements.
- Experiment without Risk: Test new ideas in a risk-free setting that mimics actual operational conditions, including the impact of different batch sizes on efficiency.
- Internalize Continuous Improvement: Learn by doing, thereby embedding a culture of kaizen and ongoing refinement.
5.2. Development Process: From Concept to Reality
Developing Get Lean was an iterative process based on continuous feedback and real-world validation:
- Extensive Pilot Testing: We conducted numerous pilot programs across different industries to gather feedback and refine the game.
- Iterative Refinement: Each cycle of development improved upon the previous one, integrating more detailed scenarios and more robust performance metrics.
- Collaboration with Experts: Input from Lean practitioners and cross-functional teams ensured that every aspect of the simulation was both practical and impactful.
- Data-Driven Adjustments: Real operational data was integrated into the simulation, ensuring that the challenges and metrics closely mirrored those encountered in real-life settings.
Get Lean is the culmination of this rigorous development process—a tool designed to make Lean principles tangible, actionable, and engaging.
6. Core Components of Get Lean
At its essence, Get Lean is a comprehensive simulation designed to provide an immersive learning experience centered around Lean Manufacturing. Its components have been meticulously developed to ensure that every aspect of the simulation contributes to a better understanding of continuous improvement.
6.1. Realistic Simulation Environments
Get Lean creates a virtual production or service environment that reflects the complexities of real-world operations. Unlike some simulations that focus on equipment breakdowns, Get Lean is process-centric:
- Workflow Optimization: Scenarios emphasize the importance of streamlining processes, eliminating waste, and achieving optimal flow.
- Inventory Management: Simulated challenges demonstrate how to balance inventory levels using just-in-time strategies and the concept of one-piece flow to reduce batch sizes and waste.
- Quality Control: The simulation includes exercises focused on maintaining high quality through standardized procedures.
6.2. Time-Pressured Decision-Making
A critical aspect of Get Lean is its focus on rapid, informed decision-making:
- Structured Rounds: The simulation is divided into time-bound rounds that mimic real production cycles.
- Urgency and Strategy: Participants must quickly analyze data and make strategic decisions to improve key metrics.
- Real-Time Feedback: Performance dashboards provide instantaneous feedback, highlighting both successes and areas for improvement.
6.3. Role-Based Collaboration
Collaboration is key in the Get Lean simulation, which mirrors the real dynamics of a lean organization:
- Defined Roles: Each team member is assigned a specific role (e.g., process manager, quality analyst) to replicate real responsibilities.
- Team Coordination: Success relies on effective communication and coordinated efforts across various functions.
- Shared Accountability: The simulation reinforces that every decision impacts the overall outcome, fostering a sense of collective responsibility.
6.4. Integrated Continuous Improvement Mechanisms
Get Lean embeds the philosophy of continuous improvement throughout the simulation:
- Iterative Learning Cycles: Post-round debrief sessions allow teams to discuss outcomes, learn from their decisions, and adjust for future rounds.
- Data-Driven Insights: Metrics and performance indicators drive home the importance of every adjustment, mirroring the Lean focus on data-backed decision-making.
- Kaizen Approach: Each cycle reinforces the kaizen philosophy—always looking for ways to improve, no matter how small the change.
For a detailed breakdown of Get Lean’s features, please visit our Get Lean – Simulation Game Overview page.
7. Integrating Lean, Six Sigma, and 5S in Get Lean
A unique strength of Get Lean is its holistic integration of key continuous improvement methodologies. By blending Lean, Six Sigma, and 5S, Get Lean offers a comprehensive training solution that prepares employees for real-world challenges.
7.1. Lean Methodologies
At its core, Lean is about eliminating waste and optimizing workflows:
- Waste Elimination: Get Lean challenges teams to identify non-value-added activities and implement solutions that remove inefficiencies.
- Flow Optimization: The simulation teaches strategies such as pull-based production and continuous process flow, ensuring that every element of the operation contributes to overall efficiency.
- Standard Work: By implementing standard work, teams can create standardized instructions that improve consistency and quality in processes, eliminating variability and waste, and leading to higher standards in outcomes.
7.2. Six Sigma Integration
While Lean focuses on efficiency, Six Sigma contributes by ensuring quality and reducing variation:
- DMAIC Cycle: Participants practice the five phases of DMAIC (Define, Measure, Analyze, Improve, Control) to systematically address process shortcomings, including understanding important lean concepts like takt time to enhance production efficiency.
- Defect Reduction: The simulation incorporates elements of statistical analysis and root cause identification to minimize defects and improve product quality.
- Quality Metrics: Real-time tracking of defect rates and performance indicators reinforces the importance of quality control.
7.3. Emphasis on 5S
The 5S framework is vital for maintaining an organized and efficient workplace:
- Workplace Organization: Get Lean includes exercises where employees sort, set in order, shine, standardize, and sustain their work environments. As part of these exercises, disorganized boxes are used to enhance engagement, with one box recommended for every three trainees.
- Standardization: Implementing standardized work practices ensures that improvements are maintained over time.
- Sustainability: The simulation emphasizes the long-term nature of maintaining order, critical for consistent performance improvement.
This integration ensures that Get Lean provides a full-spectrum approach to continuous improvement, making it one of the most comprehensive examples of lean manufacturing games available today.
8. The Strategic Benefits of Game Lean Training
Implementing a game lean training program like Get Lean offers significant strategic advantages:
- Engagement and Retention: Interactive simulations create a stimulating and fun environment, boosting employee involvement and improving retention of Lean principles through active learning.
- Accelerated Decision-Making: Time-bound scenarios develop quick, effective decision-making skills necessary for real-world operations.
- Risk-Free Experimentation: The safe environment provided by Get Lean allows for innovative problem-solving without the costs associated with failure.
- Enhanced Collaboration: Role-based teamwork fosters cross-functional communication and collective problem-solving, breaking down silos.
- Operational Gains: Measurable improvements in cycle time, defect reduction, and waste elimination directly impact the bottom line.
- Cultural Transformation: By embedding continuous improvement into daily operations, game lean training helps transform organizational culture into one of sustained excellence.
For further insights on the impact of gamified training, read about how gamification is reshaping training
9. Best Practices for Implementing Simulation-Based Lean Training
Achieving the full potential of game lean training requires a carefully planned and executed approach. Follow these best practices:
9.1. Conduct a Thorough Needs Assessment
- Evaluate Current Processes: Identify key inefficiencies and bottlenecks that hinder productivity.
- Set Clear Objectives: Establish measurable goals, such as reducing waste or increasing throughput.
- Gather Comprehensive Feedback: Involve both management and frontline staff to capture a holistic view of operational challenges.
9.2. Customize the Simulation to Your Needs
- Tailor Scenarios: Adapt the simulation to mirror the specific challenges of your business.
- Align KPIs: Integrate performance metrics that reflect your operational goals.
- Use Real Data: Incorporate actual operational data to enhance realism and relevance.
9.3. Launch a Pilot Program
- Select a Representative Group: Choose a diverse, cross-functional team to participate in the pilot.
- Run Multiple Iterative Rounds: Conduct several cycles to allow for experimentation and continuous improvement.
- Debrief and Refine: Organize structured debrief sessions to discuss outcomes and iterate improvements after each round.
9.4. Scale and Standardize Your Training
- Gradual Rollout: Expand the program incrementally, beginning with critical departments.
- Blend with Other Methods: Combine game lean training with traditional workshops and online modules.
- Monitor Continuously: Use real-time dashboards to track progress against your KPIs, adjusting the simulation as needed.
For further guidance on tailored solutions, please visit our Advanced Lean Simulation Customization page.
10. Real-World Impact and Success Stories
Organizations that have embraced Get Lean report transformational changes. Here are a few success stories that illustrate the real-world impact of game lean training:
10.1. Optimizing Process Efficiency
A significant manufacturing enterprise integrated Get Lean into its training regime. Teams identified workflow bottlenecks through simulation rounds that involved various roles, including sales, customer liaison, and operations, restructured production lines, and implemented Lean methodologies. This led to noticeable cycle time improvements and a significant operational waste reduction.
10.2. Enhancing Quality Management
A service-based organization adopted Get Lean to improve its quality control processes. In the simulation, teams practiced continuous improvement and defect reduction, learning how to identify the root causes of errors and implement corrective actions. The result was enhanced product quality and customer satisfaction.
10.3. Boosting Cross-Functional Collaboration
A multinational company used Get Lean as a tool to foster collaboration across departments. Through role-based exercises, employees from production, quality control, and management worked together to address process inefficiencies. This integrated approach broke down silos and established a culture of shared responsibility for continuous improvement.
11. Step-by-Step Guide to Implementing Get Lean
Implementing Get Lean into your training program involves a systematic, multi-phase approach:
11.1. Identify and Define Objectives
- Conduct a Comprehensive Process Audit: Examine your operations to determine areas with excessive waste, delays, or quality issues.
- Set Measurable Targets: Define specific KPIs, such as a percentage reduction in cycle time or a decrease in defect rates.
- Engage Stakeholders: Collaborate with both leadership and frontline employees to develop a unified vision of training outcomes.
11.2. Customize the Simulation Experience
- Tailor Scenarios: Adapt the simulation’s content to reflect your organization’s specific challenges.
- Integrate Your Data: Use actual performance metrics to enhance the realism of the simulation.
- Define Role-Based Modules: Ensure that each participant is assigned a role that mirrors their real-life responsibilities.
11.3. Pilot the Program
- Select a Diverse Pilot Team: Choose participants from various departments to ensure a comprehensive trial.
- Execute Multiple Rounds: Run several iterations to allow for iterative learning and strategy refinement.
- Conduct Thorough Debriefings: Analyze outcomes, discuss lessons learned, and adjust the simulation based on feedback.
11.4. Scale Up and Standardize
- Gradual Expansion: Roll out the simulation across multiple departments or locations once the pilot proves successful.
- Combine with Traditional Training: Integrate Get Lean with other learning methods for a blended approach.
- Monitor and Iterate: Regularly review KPI performance and refine the simulation as your operations evolve.
12. The Future of Game Lean in Corporate Training
The field of game lean training is continuously evolving as new technologies and methodologies emerge. Looking ahead, several trends will shape the future of simulation-based Lean training:
12.1. Immersive Technologies
- Virtual Reality (VR) and Augmented Reality (AR): Future iterations of game lean training may incorporate VR and AR, providing even more immersive and lifelike simulations. These technologies will enhance multisensory engagement and provide real-time interaction in 3D environments, where teams can draw various items like fish or pigs as part of creative activities to illustrate concepts such as standardization, process improvement, and creative problem-solving.
- Enhanced User Experience: As technology advances, the quality of simulations will improve, leading to more detailed, interactive, and realistic training modules.
12.2. Global and Cloud-Based Training Platforms
- Standardization Across Locations: Cloud-based simulations will allow organizations to deploy consistent training solutions globally, ensuring that Lean principles are uniformly adopted across international teams.
- Multilingual Support: Future solutions will likely include comprehensive multilingual support, ensuring accessibility for diverse workforces.
12.3. Data-Driven Personalization
- AI-Enhanced Analytics: Leveraging artificial intelligence, future game lean platforms will offer deeper insights into performance data, enabling personalized learning paths and continuous curriculum optimization.
- Real-Time Feedback Loops: Enhanced analytics will provide actionable insights, making every simulation cycle a stepping stone toward operational excellence.
12.4. Blended Learning Ecosystems
- Integrated Learning Platforms: The convergence of digital and traditional training methods will produce robust, scalable learning ecosystems that cater to different learning styles.
- Continuous Development: Blended learning ensures that employees receive continuous training, keeping pace with evolving Lean strategies and market conditions.
13. Conclusion – Empowering Continuous Improvement Through Game Lean
Game lean training stands as a transformative approach in the realm of corporate education. It translates complex Lean Manufacturing theories into engaging, practical simulations that drive real-world improvements. Our flagship tool, Get Lean, represents the culmination of 25 years of hands-on Lean Manufacturing experience and a dedicated six-year development cycle. It integrates Lean, Six Sigma, and 5S methodologies into a comprehensive simulation that empowers employees to optimize processes, eliminate waste, and foster a culture of continuous improvement.
Get Lean transforms the way companies implement Lean Manufacturing. It provides a safe, interactive environment where employees can make rapid decisions, work collaboratively, and learn from immediate feedback. By mimicking real operational challenges while focusing on process optimization rather than machinery failures, Get Lean demonstrates the practical benefits of Lean principles.
The benefits of adopting this game lean approach are tangible: reduced waste, shortened cycle times, improved quality, and enhanced team collaboration lead to significant cost savings and a sustainable competitive edge. Furthermore, the cultural transformation achieved through simulation-based training nurtures an environment of perpetual improvement and innovation.
Ready to transform your organization’s Lean journey? Purchase Get Lean Simulation Game today and unlock the full potential of interactive, immersive training. To learn more about the innovative features of Get Lean and how it can be customized to meet your specific needs, discover more about the game.
For additional insights into the benefits of experiential learning, explore simulation-based learning and read about how gamification is reshaping training.
Embrace the future of corporate training with game lean solutions, empower your workforce to drive continuous improvement, and secure a lasting competitive advantage through transformative, simulation-based learning.