Lean Manufacturing Games – Accelerating Continuous Improvement with Get Lean
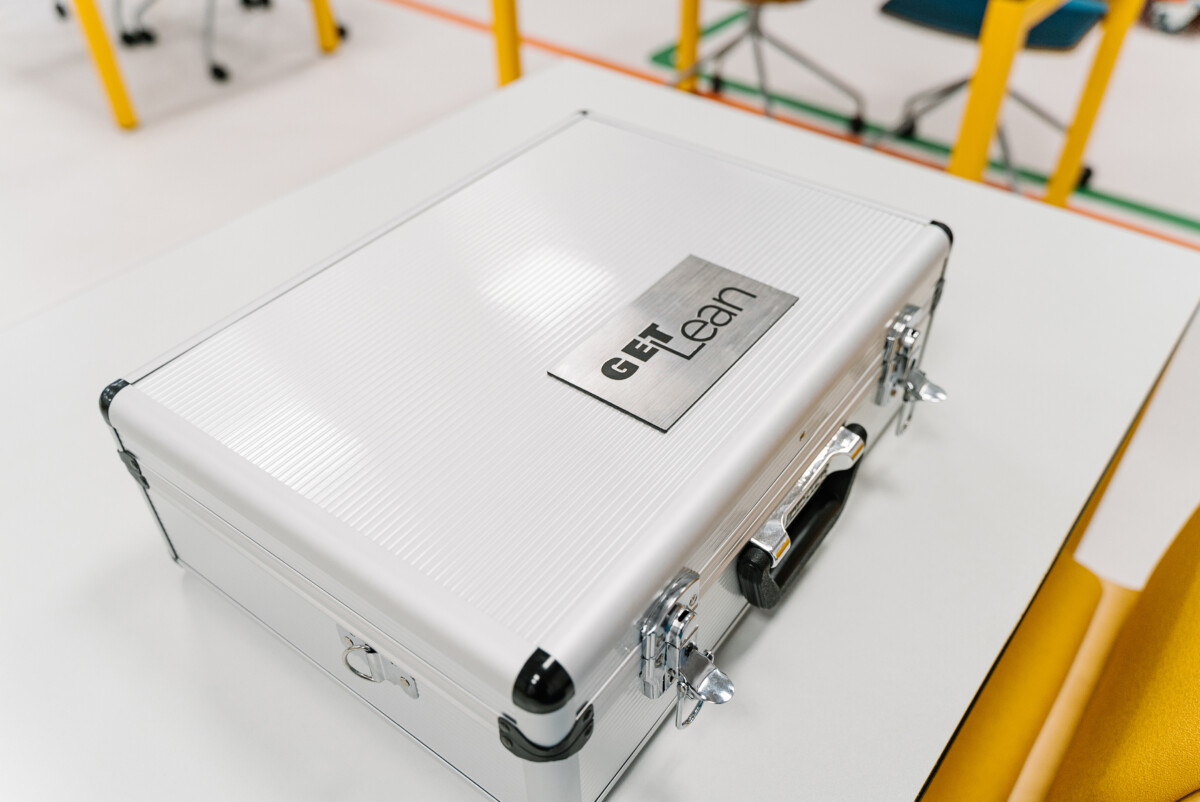
Durable and portable, this GET Lean case holds all the materials needed to run lean games that transform learning into real improvement. The aim of these lean manufacturing games is to educate players about lean processes, specifically within factory operations, illustrating how strategic tasks and improvements can lead to enhanced efficiency and waste reduction in a collaborative setting.
1. Introduction: The Future of Training
In today’s hyper-competitive industrial landscape, continuous improvement is not just a goal but a necessity for survival. Traditional training methods, such as lectures and workshops, have long struggled to bridge the gap between Lean Manufacturing theory and its practical, hands-on application on the shop floor. This is where lean manufacturing games step in to revolutionize corporate training.
Interactive simulations provide a laboratory-like environment where employees can experience real operational challenges without risks. In these simulated settings, teams experiment, make decisions, and immediately witness the outcomes of their efforts, driving faster learning and more profound insights into Lean principles. Experiential learning through Lean games is the best way to learn Lean principles, as it emphasizes active participation and enhances understanding. This innovative training method increases engagement and empowers employees to drive lasting improvements in efficiency and quality.
At the forefront of this transformation is our flagship simulation—Get Lean. Built on decades of practical experience and honed over nearly six years, Get Lean translates complex Lean methodologies into an accessible, immersive game that guides employees through the intricacies of continuous improvement.
2. Understanding Lean Manufacturing Games
Lean manufacturing games are simulation-driven training modules that immerse participants in realistic environments where they must tackle operational problems head-on. Unlike traditional training, these games require active decision-making and collaborative problem-solving. Participants engage in scenarios replicating production challenges, such as managing inventory, balancing workflows, and reducing defects. These games also help in identifying and eliminating wastes, demonstrating how different processes can waste time and resources.
Key elements include:
- Realistic Environments: Simulations mirror the challenges of actual production lines or service processes.
- Active Participation: Employees are actively involved in solving problems rather than passively consuming information.
- Immediate Feedback: Real-time dashboards display performance metrics, allowing for rapid learning and adjustment.
- Collaborative Learning: Teams work together to overcome challenges, fostering cross-functional communication and teamwork.
- Risk-Free Experimentation: The simulation environment permits safe trial and error without affecting real-world operations.
These aspects ensure that lean manufacturing games provide a dynamic, engaging platform for learning and applying Lean principles.
3. The Need for Simulation-Based Lean Training
Organizations face mounting pressure to reduce waste, optimize resources, and continuously improve processes. However, the transition from Lean theory to practical application remains a significant challenge. Simulation-based lean training meets this challenge by providing an environment in which employees can learn by doing.
Company-wide initiatives can greatly benefit from simulation-based Lean training, as it helps in overcoming resistance and fosters team engagement within the company setting.
3.1. Overcoming Learning Barriers
Traditional classroom settings often fall short of capturing the nuanced, iterative nature of Lean. Lean manufacturing games offer:
- Experiential Learning: Employees learn by actively participating in simulated scenarios, which helps them internalize Lean methodologies.
- Iterative Processes: The cyclical nature of the simulations reinforces continuous improvement and fosters a culture of kaizen (constant refinement).
- Safe Innovation: Without the fear of repercussions, employees can experiment with new ideas and strategies, accelerating their problem-solving skills.
Making the learning process fun can also help in overcoming resistance to change, encouraging team members to embrace new concepts more readily.
3.2. The Value of Experiential Learning
Research consistently shows that experiential learning significantly boosts knowledge retention and engagement. According to experts, learning by doing is far more effective than passive methods. Lean games are an excellent way to engage teams in learning new methodologies, making the process enjoyable and reducing resistance to change. For example, you can explore simulation-based learning to understand how immersive, hands-on training can transform knowledge into actionable skills.
4. My 25 Years of Lean Manufacturing Experience
4. My 25 Years of Lean Manufacturing Experie
Over the past 25 years, I have dedicated my career to implementing Lean Manufacturing strategies across numerous industries. Throughout this journey, I have witnessed firsthand the transformational power of Lean principles—when correctly applied, they reduce waste, enhance productivity, and streamline operations. Yet, a recurring issue has been the disconnect between theoretical knowledge and practical application.
Recognizing this gap, our team decided to change our approach to eliminate waste, leading to a significant reduction in the time taken to complete tasks.
In many cases, traditional training methods left employees with a superficial understanding of Lean, resulting in suboptimal process improvements. Observing this gap motivated me to pursue a different approach—one that leveraged interactive simulations to bring Lean concepts to life. This commitment laid the groundwork for the development of lean manufacturing games that could bridge the divide between classroom learning and on-the-floor execution.
5. The Journey to Create Get Lean
After years of encountering the challenges of Lean implementation, I embarked on a mission to create a solution that would fundamentally change the way organizations learn and apply Lean principles. Over a six-year development cycle, fueled by real-world project insights, I designed Get Lean—a comprehensive simulation game tailored to the needs of modern enterprises.
Foundational Goals
- Emphasize interactive team experiences to foster collaboration and engagement.
- Highlight the importance of systems thinking in understanding and applying Lean principles.
- Provide real-world scenarios from various industries to enhance problem-solving skills.
- Ensure the training is adaptable to both manufacturing and software development environments.
5.1. Foundational Goals
The primary mission behind Get Lean was to simplify the adoption of Lean by providing an immersive environment that mimics the complexities of real operations. Our objectives were to:
- Translate Theory into Practice: Enable employees to apply Lean tools in realistic scenarios. For example, simulations using Lego bricks can illustrate key Lean concepts like pull vs push, kanban, and 5S during team-building exercises.
- Reduce Resistance to Change: Create a risk-free setting where failures serve as stepping stones to improvement.
- Promote Continuous Improvement: Foster an environment where iterative learning and prompt feedback drive operational excellence. Reducing variation is crucial for process improvement, as it ensures a consistent, high-quality outcome by emphasizing the importance of standardization.
5.2. Development Process
Developing Get Lean was an iterative journey:
- Extensive Testing: We conducted numerous pilot sessions with cross-functional teams to refine the simulation.
- Real-World Data Integration: Drawing from my 25 years in Lean Manufacturing, we incorporated genuine operational challenges and metrics into the game.
- Continuous Refinement: Feedback from each iteration was used to adjust scenarios, improve user interface design, and fine-tune performance dashboards, ensuring that Get Lean delivers measurable results.
- Standard Work: Defining and documenting standard work minimizes variation in task outcomes, leading to higher quality outputs and a more uniform approach to tasks, as demonstrated through various lean games and exercises.
6. Core Components of Get Lean
Get Lean is not just a game—it’s an integrated training solution that embodies the core principles of Lean Manufacturing. Its key components include:
Improved Employee Engagement
Lean Manufacturing Games are designed to engage employees actively. These games not only make learning fun but also prove the effectiveness of Lean principles by allowing participants to demonstrate their skills in multitasking and team collaboration.
6.1. Realistic Simulation Environment
Participants are immersed in a virtual production floor that replicates real operational scenarios. These include:
- Production Bottlenecks: Players face challenges such as machine breakdowns and workflow delays, requiring them to make decisions that mirror actual production issues. By playing these interactive Lean games, participants can engage more deeply and grasp complex concepts without the pressure of traditional training methods.
- Inventory Management: The game simulates critical inventory issues, emphasizing the importance of Just-in-Time (JIT) strategies.
- Quality Control: Scenarios are designed to pinpoint defects, encouraging the application of Six Sigma techniques in real time.
6.2. Interactive Decision-Making Under Pressure
Get Lean is structured in rounds, each with a distinct set of challenges:
- Time-Bound Decisions: Similar to real operations, players must make quick decisions, reflecting the urgent pace of production.
- Strategic Choices: Participants determine resource allocation, reconfigure workstations, and apply Lean tools to optimize performance. Participants go through four rounds of specific tasks lasting 30 to 40 seconds to illustrate the differences between push and pull systems.
- Real-Time Feedback: A comprehensive dashboard provides immediate visual feedback on key performance metrics like cycle times and defect rates, enabling rapid learning and strategy adjustments.
6.3. Role-Based Team Collaboration
To mirror real organizational dynamics, Get Lean requires collaborative problem-solving:
- Defined Roles: Employees assume specific roles (e.g., process manager, quality supervisor) that contribute to holistic decision-making.
- Cross-Functional Interaction: The game promotes teamwork by having participants from various departments work together, improving internal communication and collaboration.
- Shared Accountability: Every decision impacts the entire simulation, fostering a sense of collective responsibility for continuous improvement.
Encouraged Creativity: Lean games create an interactive space for teams to learn and apply Lean concepts effectively, providing a safer environment for experimentation and innovation.
6.4. Integration of Lean, Six Sigma, and 5S
A standout feature of Get Lean is its holistic integration of multiple methodologies:
- Lean Principles: Focuses on waste elimination and process optimization.
- Six Sigma Techniques: Incorporates DMAIC (Define, Measure, Analyze, Improve, Control) for defect reduction and quality improvement.
- 5S Methodology: Emphasizes workplace organization and standardization, promoting operational efficiency.
Together, these components form the backbone of our lean manufacturing games, ensuring that participants gain a comprehensive understanding of process improvement and operational excellence.
For a detailed description of Get Lean’s features, check out our Get Lean – Simulation Game Overview page.
7. Benefits of Lean Manufacturing Games
Implementing lean manufacturing games such as Get Lean offers wide-ranging benefits for organizations:
Company-wide initiatives can significantly benefit from Lean games by improving internal processes and fostering team engagement.
7.1. Improved Employee Engagement
Interactive simulations demand active involvement, which leads to higher engagement levels compared to traditional training:
- Active Learning: Employees are continuously involved in decision-making processes.
- Enhanced Focus: The immersive environment captures attention and reduces distraction.
- Higher Retention: Participants retain Lean principles better through experiential learning.
Additionally, the digital format of Lean games allows for remote accessibility and the ability to track performance metrics, making it a viable alternative to traditional physical games. Users can engage with the application against the computer, providing a flexible and measurable learning experience.
7.2. Accelerated Learning Curve
Real-time feedback and iterative learning cycles shorten the time required to master complex Lean methodologies:
- Immediate Insights: Visual performance metrics help employees understand the impact of their decisions on efficiency.
- Rapid Iteration: Continuous rounds of gameplay enable quick refinement of strategies and concepts.
- Practical Knowledge Application: The hands-on experience ensures that theoretical knowledge is effectively translated into actionable skills. Participants might also draw various representations, such as fish or other objects, as part of the simulation to highlight creativity and understanding of customer specifications.
- Engaging Visual Content: Videos can be a useful resource for teaching and learning Lean principles, providing engaging visual content that demonstrates various Lean games and concepts effectively.
7.3. Safer Environment for Experimentation
One of the critical obstacles in adopting Lean is the fear of failure. Lean manufacturing games eliminate this barrier by offering a risk-free environment:
- No Real-World Consequences: Errors during the simulation carry no financial or operational penalties.
- Encouraged Creativity: Employees can explore and test unconventional strategies without fear.
- Resilience Building: Learning from mistakes in a controlled setting fosters a culture of continuous improvement.
7.4. Enhanced Teamwork and Cross-Functional Collaboration
By design, lean manufacturing games require collaboration:
- Improved Communication: Team-based challenges lead to better information flow and cooperation.
- Unified Vision: Collaborative problem-solving creates a shared commitment to continuous improvement.
- Stronger Interdepartmental Bonds: Breaking down silos enhances overall operational efficiency.
7.5. Tangible Operational Improvements
The ultimate goal of Lean is to drive measurable performance improvements:
- Reduced Waste: Employees learn to identify and eliminate non-value-added activities, leading to cost savings.
- Shorter Cycle Times: Optimized workflows mean faster production and reduced downtime.
- Improved Quality: Continuous monitoring and iterative refinement lead to a reduction in defects and enhanced product consistency.
8. Best Practices for Implementing Simulation-Based Lean Training
Implementing lean manufacturing games requires a strategic, structured approach to ensure maximum impact:
Conduct a Thorough Needs Assessment
Before diving into any Lean game or simulation, it’s crucial to understand the specific needs and challenges of your organization. This will help tailor the activities to address those areas effectively. Providing detailed instructions for Lean games is essential to ensure participants understand the steps they need to follow, fostering clarity and a deeper understanding of Lean principles during hands-on experiences.
8.1. Conduct a Thorough Needs Assessment
Begin by identifying core operational pain points:
- Analyze Processes: Use performance metrics to pinpoint areas for improvement.
- Define Clear Objectives: Establish measurable targets—e.g., decreasing defect rates or lowering production time.
- Engage Stakeholders: Involve managers and frontline staff to align the simulation with real-world needs. One set of clients re-evaluated their processes during a simulation called The Ball Game, streamlining operations by minimizing waste and improving efficiency. The game also illustrates the differences between push and pull systems, providing hands-on exercises that help participants understand Lean concepts through practical applications.
8.2. Customize the Simulation
Adapt lean manufacturing games to fit your organization’s unique requirements:
- Tailor Scenarios: Modify game modules to reflect your specific production challenges.
- Adjust Performance Metrics: Set KPIs that accurately mirror your organizational goals.
- Integrate Operational Data: Enhance realism by incorporating your own metrics and process data.
Align with Strategic Objectives:
- Customize the Simulation: Ensure the game aligns with your strategic objectives by tailoring it to your specific needs. Lean principles, originally developed for manufacturing, can also be effectively applied to software development. This comparison highlights how both industries can benefit from Lean practices, despite their different workflows.
8.3. Launch a Pilot Program
Pilot programs allow you to refine the simulation before a full-scale rollout:
- Select a Cross-Functional Team: Ensure representation from various departments.
- Run Multiple Rounds: Use iterative cycles to gather robust feedback and fine-tune the experience. Team-based activities around a table can help identify inefficiencies and improve collaboration.
- Debrief Thoroughly: Hold structured debriefing sessions to convert simulation experiences into actionable improvements.
8.4. Scale Your Training Program
After a successful pilot, expand the simulation program organization-wide:
- Gradual Rollout: Begin with key departments and expand gradually.
- Integrate with Existing Programs: Combine lean manufacturing games with traditional training for a blended learning approach.
- Continuously Monitor Performance: Regularly review KPIs to gauge effectiveness and adjust strategies as needed.
9. How Get Lean Revolutionizes Lean Learning
Our innovative solution, Get Lean, stands as a testament to the power of lean manufacturing games. Built on 25 years of practical Lean Manufacturing experience and a dedicated six-year development cycle, Get Lean integrates the most effective Lean, Six Sigma, and 5S tools into one immersive simulation.
The Lean Lego Game is a hands-on activity that demonstrates work cell design and optimization. Additionally, paper exercises, such as paper airplane simulations and making pamphlets, can effectively illustrate Lean concepts like process efficiency and standard work.
9.1. The Unique Edge of Get Lean
Real-World Inspired Scenarios: Every module in Get Lean is designed based on actual operational challenges encountered over decades of Lean projects.
Role-Based Gameplay: Employees assume real-life roles within the simulation, enhancing cross-functional collaboration and empathy towards different operational challenges.
Immediate, Actionable Feedback: With comprehensive dashboards tracking cycle times, defect rates, and overall productivity, participants receive prompt insights that accelerate learning. Assessing performance from the very beginning of the activity is crucial to identify areas for improvement and efficiency.
Holistic Integration: Get Lean fuses Lean, Six Sigma, and 5S principles to provide a full-spectrum training experience. This integration ensures that teams learn not only to eliminate waste but also to maintain quality and optimize every aspect of the production process.
9.2. Proven Results with Get Lean
Organizations that have implemented Get Lean report:
- Significant Waste Reduction: The simulation enables teams to identify inefficiencies and eliminate excess, directly affecting the bottom line.
- Enhanced Productivity: Streamlined workflows and reduced cycle times translate into faster, more efficient production processes.
- Improved Quality and Consistency: With tools from Six Sigma, participants learn to minimize variability and enhance product quality.
- Stronger Collaborative Culture: By fostering open communication and teamwork through role-based exercises, Get Lean builds a unified, motivated workforce.
For more detailed information on Get Lean’s features and its transformative impact, please visit our Get Lean – Simulation Game Overview page.
10. Step-by-Step Guide to Integrating Get Lean
Implementing a lean manufacturing game like Get Lean within your organization involves several key steps:
First, you need to identify the objectives of the game. Are you looking to improve efficiency, reduce waste, or enhance team collaboration? Once the objectives are clear, you can tailor the game to meet these goals.
Next, focus on work cell design and optimization. This is where the concept of one-piece flow becomes crucial. One-piece flow is essential in reducing batch sizes and improving efficiency, which are key aspects of Lean methodology. By organizing work cells to support one-piece flow, you can significantly enhance productivity and minimize waste.
Finally, ensure that all participants understand the rules and objectives of the game. This will help them engage more effectively and apply Lean principles in a practical setting.
Under ‘Global Training Solutions,’ trainers play a crucial role in guiding sessions and implementing participative games. They facilitate learning and improvement initiatives, enhancing participants’ understanding of operational excellence principles.
10.1. Identify and Define Objectives
- Pinpoint Operational Inefficiencies: Analyze key processes to identify areas of waste or bottlenecks.
- Set Measurable Targets: Define clear goals, such as reducing production time or lowering defect percentages.
- Engage Key Stakeholders: Gather input from senior management and frontline staff to ensure alignment with organizational needs.
10.2. Customize the Simulation
- Tailor Scenarios: Adjust game modules to simulate your specific operational challenges.
- Integrate Organizational Data: Use your own KPIs and performance metrics to enhance realism.
- Align with Strategic Objectives: Ensure that each simulation round helps move the organization closer to its broader Lean goals.
10.3. Conduct a Pilot Program
- Select a Diverse Team: Choose participants from various departments to represent different operational perspectives.
- Run Iterative Sessions: Conduct multiple rounds of simulation to allow teams to learn, adapt, and refine their strategies.
- Debrief and Gather Feedback: Hold structured debrief sessions to capture insights and adjust the simulation for maximum impact.
10.4. Scale Up and Standardize Training
- Gradual Expansion: Roll out the simulation program across multiple sites or departments.
- Blend Training Modalities: Integrate lean manufacturing games with existing training programs for a holistic approach.
- Continuously Monitor KPIs: Establish regular review sessions to measure progress against your objectives and refine training as needed.
To explore tailored solutions that meet your unique needs, visit our Advanced Lean Simulation Customization page.
11. Work Cell Design and Optimization
Work cell design and optimization are critical components of Lean manufacturing, as they play a pivotal role in reducing waste and improving efficiency. A well-designed work cell can help teams work more efficiently and effectively, which is why it’s essential to consider factors such as batch sizes, takt time, and customer demand when designing a work cell.
The Lean Lego Game is a fantastic tool for teaching teams about work cell design and optimization, as it allows them to experience the benefits of a well-designed work cell firsthand. In a work cell, team members collaborate to complete a task, making it crucial to consider the skills and strengths of each team member when designing the work cell.
The goal of work cell design and optimization is to create a smooth flow of work, which is why it’s essential to identify and eliminate waste in the process. By using Lean principles, such as pull systems and continuous improvement, teams can optimize their work cells and enhance their overall efficiency and productivity.
By integrating Lean principles into work cell design, organizations can create a streamlined and efficient workflow that meets customer demand while minimizing waste. This approach not only improves operational efficiency but also fosters a culture of continuous improvement, driving long-term success and sustainability.
11. The Future of Lean Manufacturing Games
As technology and industry practices evolve, so too will the landscape of lean manufacturing games. In the near future, we expect to see:
- Incorporation of Immersive Technologies: Virtual Reality (VR) and Augmented Reality (AR) will create even more lifelike, engaging simulations.
- Global Training Solutions: Cloud-based, multilingual platforms will allow companies to standardize training across regions.
- Data-Driven Optimization: Advanced analytics and AI will further refine simulation outcomes, providing detailed insights into operational performance.
- Blended Learning Ecosystems: Combining lean manufacturing games with traditional and e-learning methodologies will yield comprehensive, scalable training systems that adapt over time.
These advancements will continue to drive the adoption of lean manufacturing games as the standard for corporate training in continuous improvement and process optimization.
12. Conclusion – Achieving Sustainable Operational Excellence
Lean manufacturing games are not just a training tool; they represent a fundamental shift in how organizations approach learning and operational excellence. Our flagship solution, Get Lean, encapsulates over 25 years of real-world Lean Manufacturing expertise and a dedicated six-year development process. It integrates Lean, Six Sigma, and 5S into an immersive simulation that empowers employees to identify waste, streamline processes, and continuously improve operations in a risk-free environment.
Get Lean delivers tangible benefits such as reduced waste, shorter cycle times, higher quality, and enhanced teamwork. Moreover, the simulation cultivates a culture of continuous improvement, ensuring that Lean becomes an integral part of your organizational DNA. With each simulation round, employees are encouraged to think critically, adapt strategies based on real-time feedback, and collaborate effectively to drive sustainable change.
Are you ready to revolutionize your training strategy and unlock your organization’s potential? Purchase Get Lean Simulation Game today and start your journey toward operational excellence. To learn more about the innovative features of our solution and how it can be tailored to your specific needs, discover more about the game.
For further insights on the impact of experiential learning and gamification, consider exploring resources like this comprehensive article on experiential learning and this resource on gamification in corporate training.
Lean manufacturing games such as Get Lean are paving the way for a new era in corporate training—one that is interactive, iterative, and deeply engaging. Embrace the future of Lean training, empower your employees, and achieve lasting competitive advantage through continuous improvement.